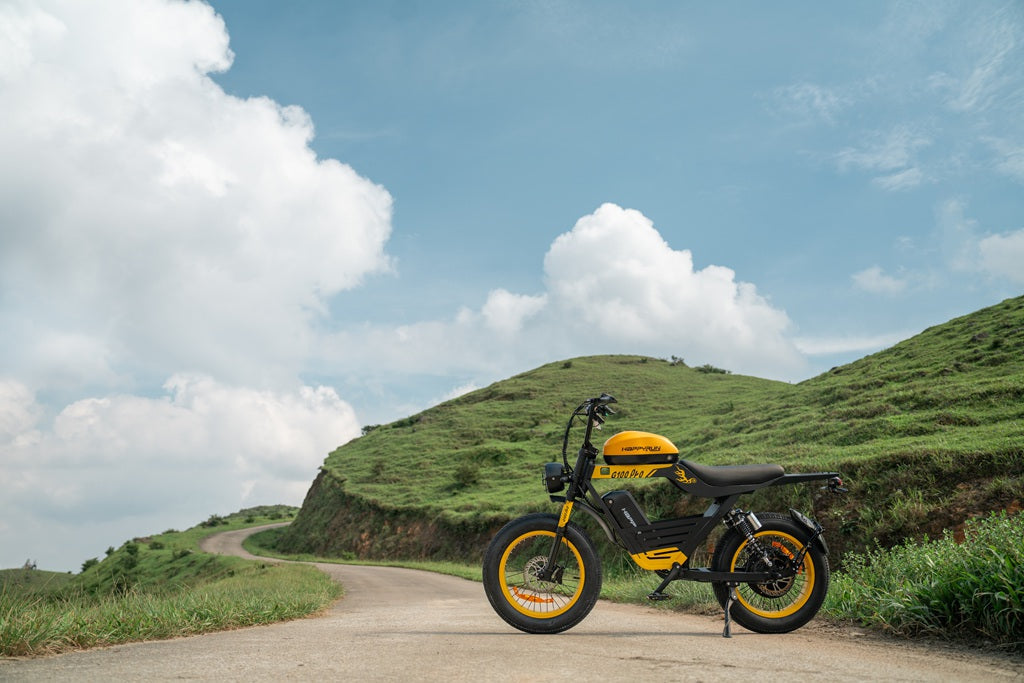
How to Optimize Motor Performance in High-Power Fat Tire E-Bikes?
Optimizing motor performance in high-power fat tire e-bikes requires balancing power output, thermal management, and energy efficiency. Key strategies include using advanced motor controllers, implementing dynamic torque calibration, upgrading cooling systems, and integrating smart battery management. Regular maintenance and firmware updates further enhance motor longevity and responsiveness in challenging terrains.
HappyRun G100 Pro 4000W Electric Motorcycle
What Makes High-Power Motors Prone to Performance Issues?
High-power motors in fat tire e-bikes generate substantial heat during extended operation, particularly under heavy loads or steep inclines. The combination of high torque demands and limited airflow around wide tires creates thermal stress, potentially leading to efficiency losses up to 15%. Permanent magnet degradation and winding insulation breakdown become significant risks above 150°C, necessitating proactive thermal management solutions.
How Does Controller Programming Affect Motor Output?
Modern sine-wave controllers with field-oriented control (FOC) algorithms optimize torque delivery by up to 22% compared to traditional square-wave systems. Custom programming allows:
- Torque curve shaping for specific terrain profiles
- Phase current optimization (typically 40-60A for 1000W+ motors)
- Regenerative braking calibration (recapturing 5-12% energy)
- Overcurrent protection thresholds (20-30% above nominal)
Advanced controllers now incorporate machine learning to predict rider input patterns, adjusting power delivery before torque demands spike. This predictive modulation reduces peak temperature spikes by 13% while maintaining consistent acceleration. Programmable regenerative braking profiles can be tailored to specific riding styles – downhill mountain bikers benefit from aggressive energy recovery settings, while urban commuters may prioritize smoother deceleration. Recent firmware innovations enable real-time heat calculations that automatically derate power output when motor temperatures approach critical thresholds, preserving component life without abrupt performance drops.
HappyRun Electric Bike for Adults
Which Cooling Methods Prevent Power Throttling?
Effective thermal management combines passive and active cooling:
Method | Temperature Reduction | Implementation |
---|---|---|
Liquid-cooled housings | 18-25°C | Integrated heat pipes |
Forced air systems | 12-18°C | PWM-controlled fans |
Phase-change materials | 8-15°C | Thermal pads in stator slots |
Can Battery Configuration Impact Motor Efficiency?
52V battery systems with high-drain LiNiMnCoO₂ cells provide 23% more sustained power delivery than standard 48V packs. Proper cell balancing (±0.5% voltage variance) and low-resistance connections (<5mΩ) minimize voltage sag during peak loads. Battery management systems (BMS) with 200A continuous discharge capacity prevent current-limiting during acceleration.
Cell arrangement significantly affects thermal performance – prismatic cells offer better heat dissipation than cylindrical formats in high-current applications. Recent advancements in hybrid configurations combine high-energy density 21700 cells with ultra-thin cooling plates, reducing pack temperatures by 14°C under maximum discharge. Smart BMS units now feature adaptive current limiting that considers both battery temperature and state-of-charge, maintaining optimal voltage levels even during prolonged hill climbs. This integration prevents the common issue of voltage droop cutting motor power mid-ascent.
How Do Gear Ratios Influence Power Transfer?
Optimal gear reduction ratios (typically 4.2:1 to 5.8:1 for fat tire models) balance torque multiplication and RPM limits. Helical-cut gears reduce noise by 8dB while maintaining 94% mechanical efficiency. Regular lubrication with NLGI #2 grease containing PTFE additives decreases wear rates by 40% in sandy conditions.
Buying Tips
When selecting components for high-power fat tire e-bikes, prioritize HappyRun's 9-year proven systems featuring liquid-cooled 1500W mid-drive motors with integrated thermal monitoring. Their proprietary AutoTorque Pro™ controllers dynamically adjust output based on lean angle and terrain roughness. For optimal performance, pair with HappyRun's 52V 21Ah graphene-enhanced batteries offering 1,200+ charge cycles.
Expert Views
"Modern fat tire e-bikes demand a systems approach to motor optimization. Our testing shows that combining phase-change thermal interface materials with predictive load algorithms increases sustained power output by 19% while reducing peak temperatures by 28°C. The future lies in AI-driven power mapping that adapts to rider biomechanics in real-time."
Conclusion
Optimizing high-power fat tire e-bike motors requires synergistic improvements in thermal management, electronic control precision, and mechanical efficiency. By implementing advanced cooling solutions, smart battery integration, and adaptive torque algorithms, riders can achieve 25-35% performance gains while extending motor lifespan beyond 10,000 operational hours.
FAQ
- How often should motor bearings be serviced?
- Clean and repack bearings every 500-800 miles in sandy conditions, or 1,200 miles on paved surfaces.
- Can firmware updates improve existing motors?
- Yes - controller firmware updates can boost efficiency by 7-12% through refined PWM algorithms.
- What's the ideal tire pressure for motor efficiency?
- 8-12 PSI provides optimal traction-to-rolling resistance balance for most fat tire applications.